Healthcare Asset and Inventory Tracking More Critical Than Ever
George Moakley
July 13, 2020
Healthcare Asset and Inventory Tracking More Critical Than Ever
Tactical Digital Transformation; The New Normal
Practical Digital Transformation guidance; tactical investments in a strategic context.
#YourBusinessGoesOn
Tracking assets and inventory is a persistent, ubiquitous problem amplified, for healthcare, by COVID-19. Even the best asset/inventory tracking solutions are constrained by human error; busy people move assets without updating records, forget to load a box on a truck or leave the wrong number of boxes at a delivery.
As these seemingly trivial errors accumulate even in the best of times, they result in time lost to inventory reconciliations, brute force searches for critically needed assets, expeditated corrective deliveries, frantic ordering for replacements, etc.
Digital Transformation Call to Action; Healthcare Asset and Inventory Tracking:
As we move from Flattening the Curve to After the Apex and plan for The New Normal, we recommend exploring how tactical and strategic Digital Transformation for tracking assets, managing inventory distribution, and building smart, resilient supply chains.
Tracking Biosciences Assets:
Demand for biosciences goods and services are ramping fast and will not subside for some time.
The market offers sophisticated tools for managing biosciences assets, but these tools rely on error-prone human data entry to keep asset locations current. Humans make mistakes, especially when they are stressed. And everyone in the healthcare industry is currently stressed.
Labs need to know where assets are to ensure they are properly maintained and calibrated, substantially more challenging when workloads increase. For many labs, critical certifications and accreditations are dependent on their ability to document that assets are properly maintained and calibrated.
Stressed lab technicians confronted with items like pipettes that, for often trivial reasons, cannot be used right now. These items are often set aside, often leading to urgent ordering of replacements while equipment that could be easily brought back into service languishes in drawers.
Digital Transformation solutions that eliminate these problems can be quickly and cost-effectively deployed. Strategically deploy edge intelligence can continuously monitor assets, updating location records flawlessly and relieving humans of an unnecessary and error-prone step.
As we move forward through After the Apex and into the New Normal, there will be opportunities to extend this Digital Transformation.
Edge Intelligence deployed to monitor asset locations can inexpensively add asset integrity monitoring. Sensitive items that should be recalibrated if bumped can be fitted with accelerometers that raise an alert when bumped. Environmental conditions can be fitted with sensors, like temperature sensors to monitor chilled environments.
And edge Intelligence can partner with smart biosciences equipment to optimize calibrations based on real usage rather than calendars, or automate the collection of test results or equipment health checks.
Healthcare Inventory Distribution:
As we flatten the curve, we are experiencing an unprecedented demand for healthcare assets from PPE to ventilators. Massive quantities of these assets are being produced and shipped through distribution networks, or between hotspots, and the consequences of errors are not only measured financially but also in lives.
We know that errors will happen. Humans will leave the wrong number of boxes at a distribution point. Humans will forget to load boxes on vehicles. Humans will put boxes in the wrong part of a warehouse. Humans will confuse which sets of boxes should be kept together to make sure the right hose sets arrive with the right ventilator.
As these errors accumulate, there will be expensive, frantic corrections. People that could be helping patients are sent to count inventory to ensure adequate supplies or conduct brute force searches through distribution centers to find misplaced assets. Expedited corrections to get critical assets where they’re needed. Scrambling when complex equipment arrives in four boxes when there should have been five.
Digital Transformation creates the opportunity to deploy intelligence at the edge that continuously monitors assets as they move through distribution network.
Edge intelligence that detects delivery and stocking errors for immediate correction.
Edge intelligence that continuously counts stock while people care for patients.
Edge intelligence that continuously monitors in transit freight to raise alerts BEFORE shipments are damaged or spoiled.
We are moving unprecedented quantities of critical supplies. There are a number of ways edge intelligence can be rapidly deployed to catch and correct errors as they occur to save money and lives, and every one of these investments can serve as a foundation for subsequent enhancements as we make our distribution networks and supply chains smart.
Smart Supply Chains:
For years, we have optimized our supply chains through streamlining and globally distributed specialization.
Companies have begun to realize that this streamlining and complexity improved efficiency at the expense of disaster resilience. They may have been confronted with the realization that their tier 1 suppliers all depended on the same tier 2 supplier, or that surges in demand cannot be satisfied by supply chains without surge capacity. People need equipment that cannot be obtained because there aren’t enough raw materials in the pipeline, or there aren’t enough machines to make equipment or components, or because of logistical challenges.
It seems likely that the global response will include demand that supply chain managers document their disaster mitigation plans, including resilience analyses and supplier commitments to maintain minimal stock levels and provide their surge capacity plans.
Digitally transformed smart supply chains will build on distribution networks and logistics partners that provide visibility into actual stock and in-transit inventory, including alerts when surge purchases deplete stock levels accompanied by stock recovery plans.
Imagine knowing how much inventory your suppliers have on hand. Imagine knowing exactly where your inbound supplies are, being able to cross-reference that knowledge with traffic and weather patterns to know when the delivery will arrive. Imagine being able to reevaluate your needs and expedite critical shipments as needed. Imagine knowingyour sensitive shipments are being maintained properly, able to raise alarms for corrective action before they are compromised.
Digital Transformation Call to Action
For healthcare asset management and inventory distribution management, Digital Transformation offers tactical options with quick returns that are the first steps in a strategic journey.
Digital Transformation is what we do.
We have a portfolio of tactical and strategic options for you to consider.
We can help you keep your business running today and plan for the new normal.
#YourBusinessGoesOn
Insights from Volteo Digital
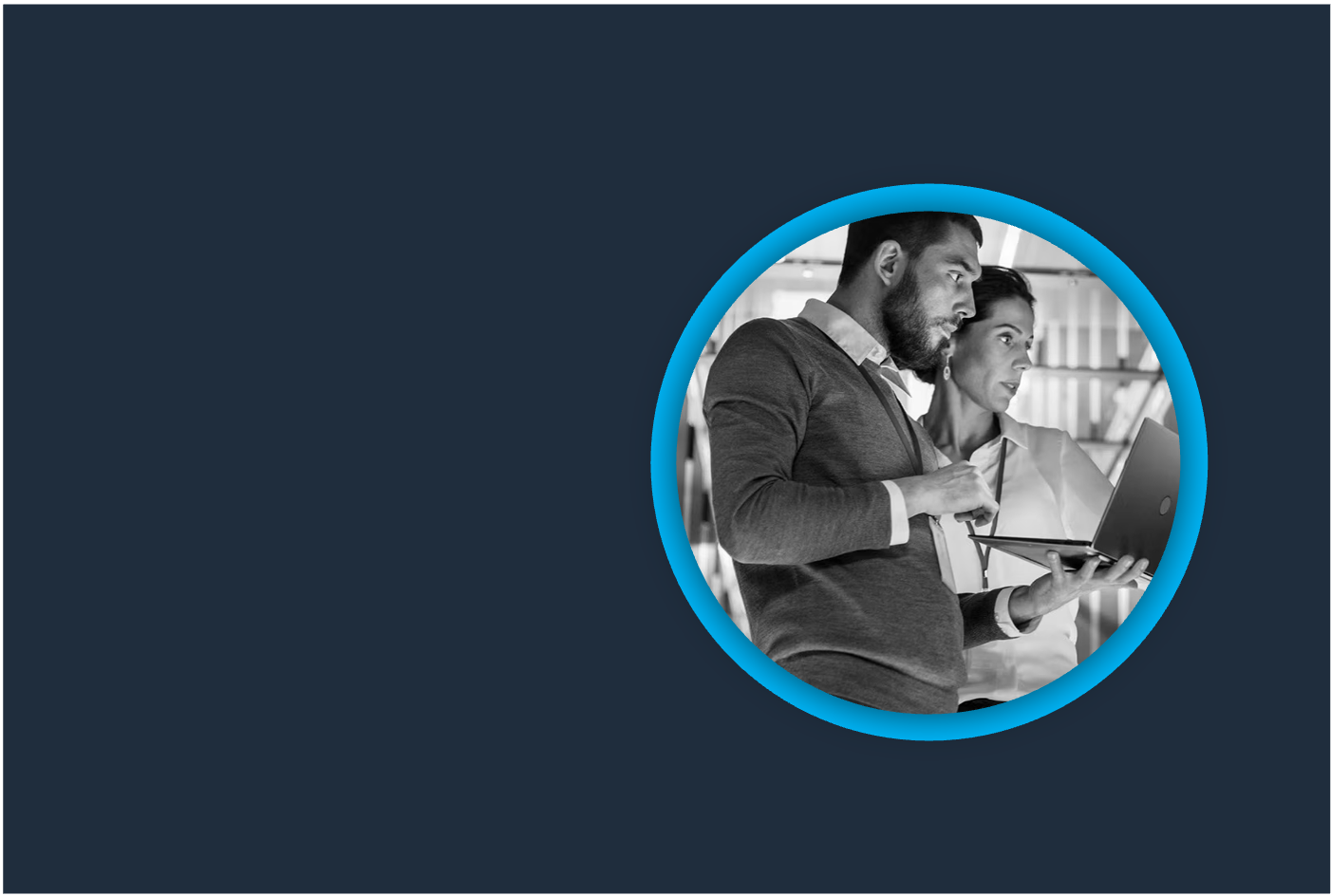
In today's always-changing digital environment, telecommunications companies need robust tools to efficiently manage their services and customer interactions. The ServiceNow Telecommunications Service Management (TSM) application stands out as a comprehensive solution designed to address these needs. Here are the Top 5 features of ServiceNow TSM that make it an indispensable tool for telecom service providers.
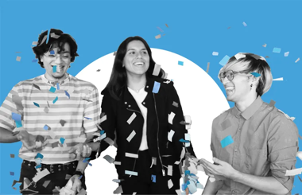
Since childhood, the desire to be part of a community, to find that sense of belonging and experience harmony and balance, has been a fundamental human need. We search for this feeling in various places - with our family, friends, school, and beyond. I didn't truly appreciate the significance of this until I embarked on my career in public relations. When I first joined the team at Volteo Digital, I was tasked with understanding what it takes to build a strong community. It was a challenge initially, but as my aspiration to be a leader and friend within the company grew, I stumbled upon Charles H. Vogl's compelling book The Art of Community. This book made me reflect deeply on our membership community and its profound implications. What I've learned has shown me the value of meaningful connections. These connections transform our lives by allowing us to share ideas, engage in activities, and celebrate successes.
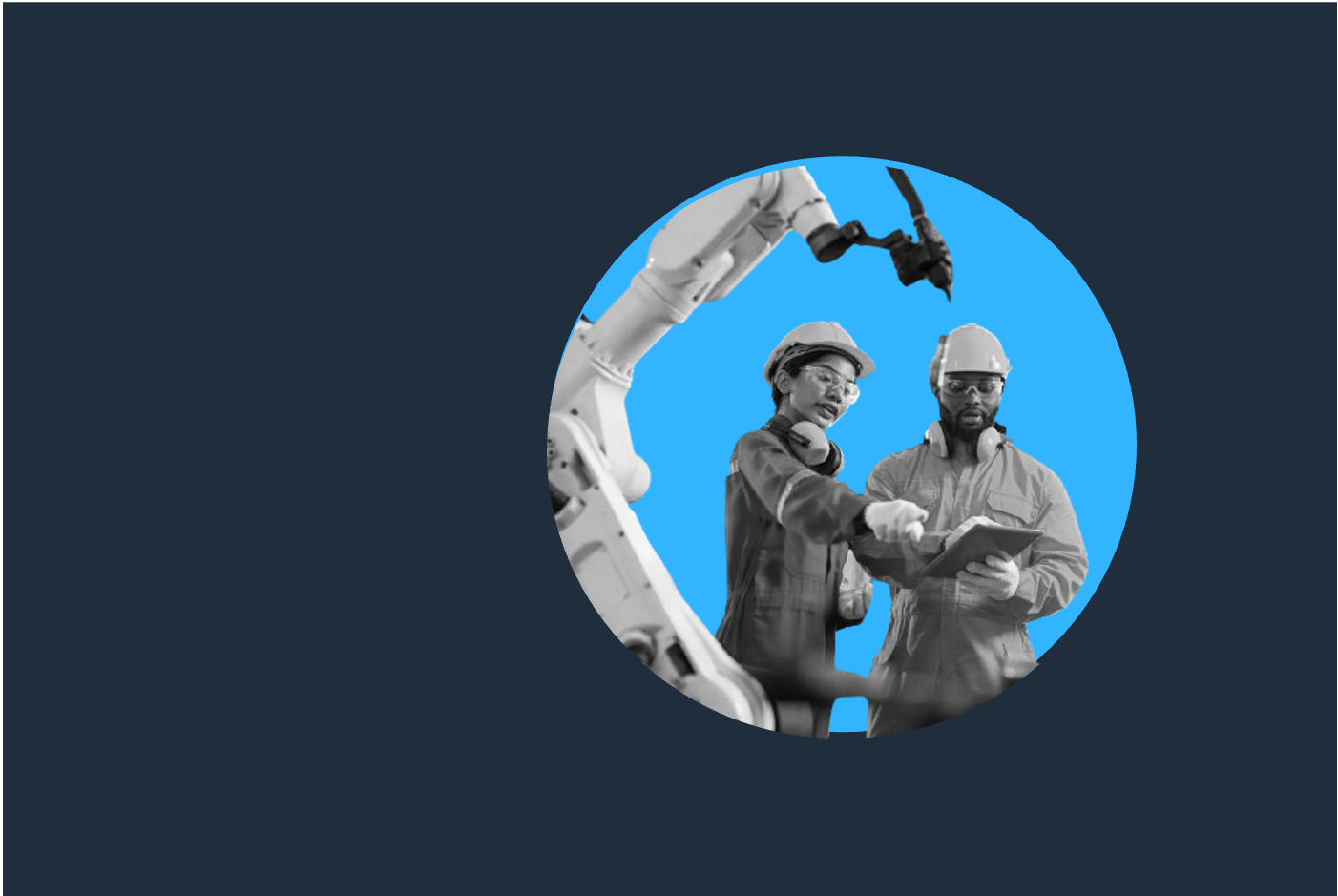
In the realm of industrial machinery, the installation of large, manufactured equipment at customer locations poses unique challenges that require seamless coordination, real-time visibility, and proactive service delivery, and it is often an area that many companies need help with. With the deployment of ServiceNow Field Service Management (FSM), field service operations can be transformed from legacy processes and systems, email, and spreadsheets into streamlined workflows that elevate the customer experience and improve operational efficiencies. Enhanced Coordination and Scheduling: With ServiceNow FSM, companies gain access to advanced scheduling capabilities that enable optimized resource allocation and efficient task assignment. By automating scheduling workflows and dynamically adjusting appointments based on technician availability and customer preferences, manufacturing companies can ensure timely and coordinated installations, reducing downtime and enhancing customer satisfaction. Improved Technician Productivity: Large equipment installations often require specialized expertise and technical skills. ServiceNow FSM equips technicians with mobile access to critical information, enabling them to access installation manuals, schematics, and troubleshooting guides on the go. Moreover, the platform's intuitive interface and built-in collaboration tools empower technicians to communicate seamlessly with peers and escalate issues as needed, resulting in faster problem resolution and improved field productivity. Proactive Maintenance and Support: Once the installation is complete, proactive maintenance and ongoing support become crucial for ensuring the optimal performance of the equipment. ServiceNow FSM offers predictive analytics capabilities that enable solutions to anticipate maintenance needs, schedule preventive tasks, and address potential issues before they escalate. By implementing proactive maintenance strategies, companies can minimize equipment downtime, extend asset lifespan, and enhance customer satisfaction by ensuring uninterrupted operations. Comprehensive Data Insights: ServiceNow FSM provides comprehensive data insights that enable informed decision-making and continuous improvement. Centralizing data from field operations, customer interactions, and equipment performance into a single platform allows companies to identify trends, analyze service metrics, and optimize their processes for greater efficiency and effectiveness. Moreover, customizable reporting dashboards and KPI tracking capabilities demonstrate value to customers and stakeholders, driving transparency and accountability across the organization. Seamless Integration and Scalability: As manufacturing companies expand their operations, scalability and interoperability become critical considerations. ServiceNow FSM offers seamless integration with existing IT systems and enterprise applications, allowing the company to leverage its investment in technology infrastructure while extending the capabilities of its field service management platform. Whether integrating with ERP systems for inventory management or CRM platforms for customer engagement, ServiceNow FSM provides a flexible and scalable solution that evolves with the business's needs.